MPX chosen for safety at a chemical plant in Japan
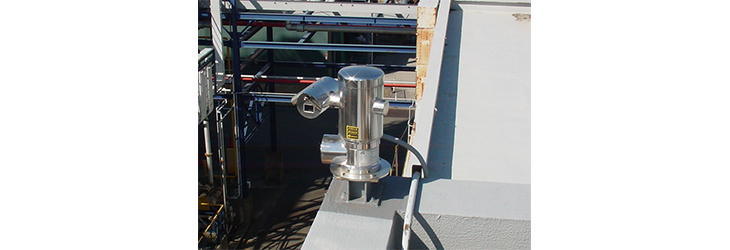
Chemical plants process raw materials derived from petroleum, acids, salts, etc. and transform them into finished products such as pharmaceuticals, detergents, products for agriculture, for the plastics industry, cars, food, textiles, cosmetics and more.
Materials are generally contained in vertical, cylindrical tanks located outdoors, under canopies, or indoors, in warehouses. Any substances which are in a gaseous state are kept in high-pressure tanks or cylinders.
If there is a leakage of volatile liquid or flammable/toxic liquefied gas from a tank or pipe then a large amount of vapour could build up and, with the right trigger, explode or catch fire.
So, its a necessity for this type of pant to implement strict prevention and safety measures.
To guarantee maximum safety and protection of persons and property, the Kawasaki chemical plant in Japan has decided to use Videotecs explosion-proof MAXIMUS MPX cameras.
At this installation, the explosion-proof MAXIMUS MPX cameras were chosen to record and identify situations which are abnormal or potentially dangerous and could, therefore, require a timely intervention. The advantage of the special MPXT thermal cameras is that they can alert somebody if temperatures get too high inside one of the tanks.
Not only that, the MPX virtual eye is able to constantly watch and manage industrial processes that are carried out in environments with high levels of toxic fumes or temperatures that are too high for people (up to 60°C).
Since devices use electrical currents, not all of them can be installed in potentially explosive environments such as chemical plants.
To this end, Videotec has produced the MPX range of cameras: a special range which has been designed to be, and certified as, explosion proof. The camera housing prevents any sparks from escaping and also avoids becoming excessively hot. To obtain the necessary certifications, these devices have been subjected to stringent tests by qualified external bodies, ensuring that they comply with international standards relating to products intended for use in potentially explosive areas (Zone 1 and 2, IIC Group T6 (gas) and Zone 21 and 22, IIC Group T85°C (dust)).
The AISI316L stainless steel used in their construction combines strength with resistance to corrosion caused by chemical agents in the air that come from the manufacturing processes which are usually present in these environments.br>
There are also cameras installed in areas across the plant which are not easily accessible, meaning that in-situ maintenance works are costly and difficult to manage. With MPX cameras, the need to intervene is virtually non-existent as they need no maintenance after installation and can be configured and upgraded remotely too.
In addition, the windscreen wiper, which is supplied as standard, coupled with the certified explosion-proof water tank, means the front glass can be cleaned remotely.
Using the high quality and very reliable products from the MAXIMUS MPX range, this chemical plants video surveillance system has successfully shown that it can reduce the potential risk of adverse events, thus contributing to the protection of people, assets, health and the environment.
Go to the product page Go to the product page
MAXIMUS MPX